Are you struggling to understand the health of your electrical assets and drowning in years of monitoring and testing data?
In the field of electrical asset management, predicting failure and risk has been the ‘holy grail’ of maintenance engineering.
Planning correctly for maintenance can save significant time and resources as well as extend the productivity of your asset.
International electrical asset expert, Luca Garagnani, explains the 3 key sources of asset health data and how you can use a revolutionary new online tool to confidently know when it’s time to schedule maintenance and testing.
“The number one problem that asset managers face is balancing the need for maintenance and production pressures, but they’re drowning in years of asset monitoring and testintg data.
In the field of electrical asset management, predicting failure and risk has been the ‘holy grail’ of maintenance engineering. Planning correctly for maintenance can save significant time and resources as well as extend the productivity of your asset.
Without analysis, more data doesn’t equal more knowledge
Engineering solutions have tended towards more testing and monitoring as an asset ages with the erroneous belief that it’s more data that leads to improved reliability. However, it’s the correct interpretation of the data that you already have that results in reliability and reduced maintenance. Essentially your strategy should be to do more with the data you have rather than increase volume of data.
Initially condition monitoring was all in the hands of expert human engineers with decades of hands-on expertise. However in recent years , especially with the development of online condition monitoring, data analytics and artificial intelligence, the result is more data but less understanding and knowledge.
The result, for today’s plant managers and supervising maintenance engineers, is increasing volumes of testing and monitoring data but often with less confidence in the interpretation.
All condition monitoring has a place in understanding asset health
For experienced engineers there is great value in integrating data from various sources, collected over time, to gain a comprehensive understanding of your asset’s health. Below are the testing and maintenance strategies you need to include in your healthy asset management mix.
Periodic onsite testing
This is the traditional model where inhouse or contractor engineering experts, like machinemonitor® , attend your site once or twice annually to conduct a suite of required testing and monitoring on your assets. The testing results are reviewed and audited by senior experts that provide maintenance and repair advice.
On site testing typically requires plant shutdown or other production modifications. The pressure to keep the plant running and producing now is often at odds with the maintenance team that are looking at the long-term health of the asset. Budgets have also been squeezed to reduce maintenance costs despite the risk to future outputs and asset longevity and reliability.
Onsite and Offsite monitoring hybrid
With the growth of computing power and data analytics many assets can produce partial discharge and other monitoring data, especially with the addition of monitoring hardware such as those supplied by E/One or Iris Power.
Many assets now come with built-in hardware producing constant monitoring data that still requires expert review and analysis in order to understand the implications for maintenance and reliability.
Data analytics and monitoring require the addition of in-person monitoring and testing to supplement and analyse data.
Continuous monitoring
The explosive growth in analytics, cyber security, online monitoring and the reduction in data storage costs have resulted in the rapid expansion of continuous monitoring. However the promise of a human-free and reliable monitoring system is still elusive. In fact these systems are expensive and produce more problems than they solve. Inexperienced engineers and busy plant and asset managers are still left to deal with an endless stream of data without the requisite ability to interpret and analyse the data.
The likelihood of false alarms is staggeringly high. Leading to unplanned shutdowns and maintenance cost blow outs.
Nonetheless all of these tools and strategies form the knowledge base for understanding the health and reliability of electrical assets and need to be carefully considered and managed in every asset maintenance plan.
Understanding the value of monitoring and testing strategies is important for determining the best and most effective testing and monitoring regime for your assets.
However, managing the volume of complex and disparate data produced over time is an equally critical issue that modern asset managers and engineering plant supervisors must deal with.
Addressing the growing problem of testing and monitoring data overload can now be managed easily with RiskMonitor PRO.
machinemonitor® invites you to try our groundbreaking online tool to instantly know the risk failure mechanism of your rotating assets.
RiskMonitor PRO is the first of it’s kind, game-changing online tool that will instantly predict the failure risk of your rotating assets. With RiskMonitor PRO you can quickly and easily aggregate all the data you have on your assets, regardless of when it was collected or by whom, to give you a clear and simple picture of the health of your asset.
machinemonitor®, electric asset optimising experts with 25 years in business, created RiskMonitor PRO as an immediate solution to a growing problem. We have a number of online and in-field testing and monitoring solutions including RiskMonitor®, that was released nearly two decades ago. We are constantly adding and refining in line with customers needs.
The game-changing online tool, RiskMonitor PRO, helps you quickly understand the leading failure mechanism for your asset and can also provide a comprehensive risk analysis easily combining all or some of the data you have available.
Make sense of your asset testing and monitoring data
✔
Understand all your monitoring and testing data
RiskMonitor PRO helps you make sense of your testing and monitoring data regardless of when or who carried out the tests or monitoring.
✔
Reduce your maintenance costs
Easily understanding the top failure mechanisms of your electrical assets and the overall health of your asset reduces the costs of maintenance.
RiskMonitor PRO takes out the ‘guesswork’ and uncertainty in planning maintenance, monitoring and testing reducing costs for unplanned or unnecessary maintenance and testing.
✔
Confidence in your asset health and reliability
You’re now in the driver’s seat with secure online access to your condition monitoring and a dedicated team of independent experts to help you make the right production decisions.
Understand your asset’s primary failure risk in under 5 minutes!
1
Gather your data
Use this checklist to gather all the data you need before getting started.
2
Enter the details into
RiskMonitor PRO
Enter the asset details via RiskMonitor PRO secure online portal.
Our proprietary algorithm developed by experts over 25 years and thousands of tests will do the work for you.
3
Immediately learn the health status of your asset;
Immediately see the top failure mechanism for your asset. Our simple traffic light system lets you see if your risk requires action.
Plus access to the full risk analysis report for a small fee.
RiskMonitor PRO working in real time using Demo machine data.
Using RiskMonitor PRO - FAQs
-
OptMonitor is the “SCADA” for Asset Managers to easily visualise the site critical asset “real” conditions, diagnostic data and engineering recommendations.
The asset conditions are evaluated by combining asset information, diagnostic tests and inspection results, continuous online monitoring data (if available) with expert engineering team oversight.
-
OptMonitor is much more than just continuous monitoring. This solution combines the data from continuous monitoring to access real-time diagnostic information that combined enhances the visibility of your assets that allows our highly-trained expert engineers to evaluate ‘real’ condition of your assets 24/7.
-
Yes, OptMonitor can be used with historical asset information, diagnostic tests and inspection results.
Our expert engineering team will evaluate the asset condition every time new test results and data is provided.
-
Yes, OptMonitor has a patent solution designed to continuously monitor online partial discharge via the electrical networks. Continuous online partial discharge data is used to monitor your asset’s conditions in real time.
-
Yes, data from third party monitoring systems can be easily integrated by the expert OptMonitor team.
We supply a cybersafe data transfer box to securely link the communication between your monitoring system and our secure server.
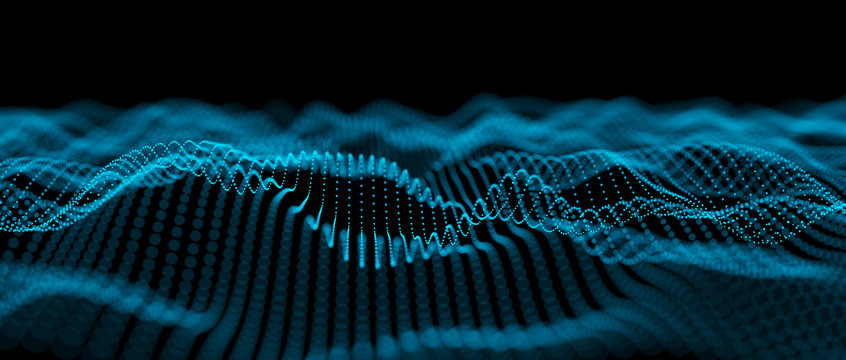